-
Automatic Bread Production Line
-
Automatic Cake Production Line
-
Automatic Toast Production Line
-
Cookie Production Line
-
Bakery Tunnel Oven
-
Baking Cooling Towers
-
Bread Proofer
-
Depanner
-
Flat Bread Production Line
-
Granola Production Line
-
Cake Depositor
-
Food Industry Conveyors
-
Baking Pan Handling Equipment
-
Rotary Rack Oven
-
Cookie Depositor
PLC Semi Automatic Bread Production Line Assembly Trolley Loader Unloader
Place of Origin | China |
---|---|
Brand Name | SAIMAI |
Certification | CE Certificate, ISO 9000 Certificate |
Model Number | Customized |
Minimum Order Quantity | 1 |
Price | Negotiable |
Packaging Details | Container/ Plastic Film Wrapping/Wooden Box |
Delivery Time | 90days |
Payment Terms | L/C, T/T |
Supply Ability | 5Set/90-120 Working Days |
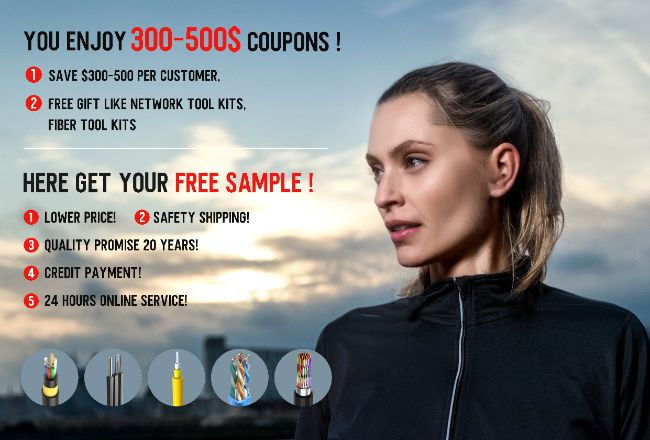
Contact me for free samples and coupons.
WhatsApp:0086 18588475571
Wechat: 0086 18588475571
Skype: sales10@aixton.com
If you have any concern, we provide 24-hour online help.
xAfter-sales Service Provided | Engineers Available To Service Machinery Overseas,Online Support,Video Technical Support,Field Installation,commissioning And Training | Material | 304SS |
---|---|---|---|
Automatic Grade | Semi-automatic | Condition | New |
Warranty | 1 Year | Size | Custom Made |
Highlight | PLC Semi Automatic Bread Production Line,304SS Automatic Bread Production Line,304SS bread production equipment |
Commercial Assembly Production Line Bakery Equipment Semi-Automatic Bread Production Line
This is a custom-made turnkey project designed for making various types of bread.With regard to the client´s need, type of the production and the selected equipment we are capable to supply these lines as semi-automated and but also as fully automated.
Trolley loader
After dough preparation and make-up line, the baking pan with dough pieces are fed into trolley automatically by using a auto trolley loader for people push them to a static proving room.
Trolley unloader
After proofing, the pan goes down from trolley via auto trolley un-loader and infeed to oven.
Tunnel oven
Function:
The function of the baking oven is fully automatic from spreading batter on the plates through until baked wafer sheets come out of the oven.
Baking is even and produces good quality wafer sheets for next procedure.
In PLC there is PID controller which is used for controlling the temperature of the baking plates
automatically .
The collection of required signal of PID is supplied by infrared sensor .
The oven status display and the data reset are supplied by a touch screen, all motor have the
starting current protection and thermal overload protection.
1
|
Oven Frame
|
GB steel with high-temperature silver paint on the surface
|
2
|
Baking Tongs
|
Grey Cast Iron
|
3
|
Plates
|
Special Heat- Resisting Cast Iron
|
5
|
Thickness of the Wafer Sheet
|
2.5mm~ 2.7mm
|
6
|
Weight for wafer sheet
|
45grams~60grams( adjustable)
|
7
|
Baking Plates Temperature Adjustable
|
Normal Temperature to 200℃
|
8
|
Main Electrical Machine
|
380V, 3kW
|
9
|
Production Capacity
|
24~28PCS /min
|
10
|
Mixing Pump Machine
|
380V, 0.75kw
|
11
|
Dimensions
|
10450×1620×2200 (L*W*H)
|
12
|
Main Feature
|
With Automatic clean device for wafer wastage
|
Needle Depanner/suction depanner/ flip-over depanner/push-bar depanner ( optional)
After baking, the suction depanner/needle depanner/flip –over depanner will take the products out from moulds. The baked products are cooled by spiral cooler and the empty pans return through the pan cooling tunnel to the dough positioning and panning machine. And enter into next cycle.
1. The Needle Depanner is designed for products that need extra care or with fillings inside, where vacuum depanner is not applicable.
2. The pans are positioned under depanner with the help of sensors and cylinder clamps. By means of pick and place, the needles are pushed into the products then move onto the cooling belt where the products are released gently.
Cooling conveyor
1. PLC systems can monitor faults and showing alarm information in English according to the customer’s requirement. It has an open communication interface for the internet and is free to connect with other controlled systems and computer systems.
2. Incorporated the design of Europe and Japan into our equipment. Maximum reduce the cost of labor and realize real automation.
3. According to the workshop area and the requirement of manufacturing to perfectly design the size and structure.